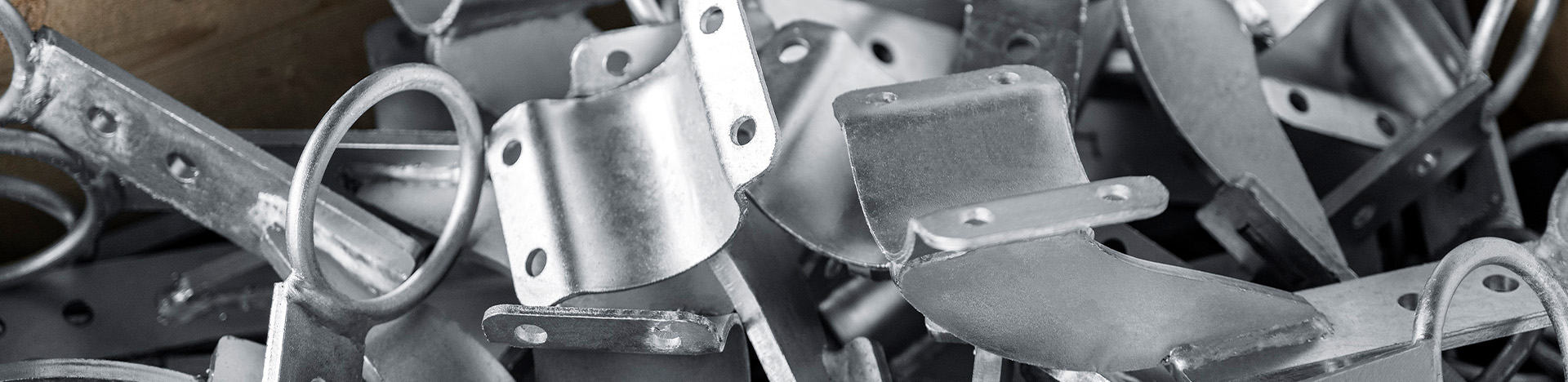
Centrifugal galvanizing: Precise protection for small parts
Centrifugal galvanising is particularly recommended as reliable corrosion protection for small parts such as screws, nuts and bulk goods, as well as for products with special surface requirements. This method ensures that even the smallest components are effectively protected against corrosion without losing functionality or accuracy of fit.
In the high-temperature/spin galvanising process, we subject your steel products to careful, multi-stage pre-treatment. The aim is to achieve a uniform surface finish and a perfect fit. During the centrifugal galvanising process, excess zinc is automatically removed, ensuring a clean and precise coating.
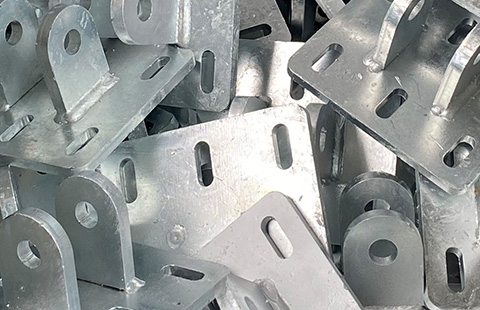
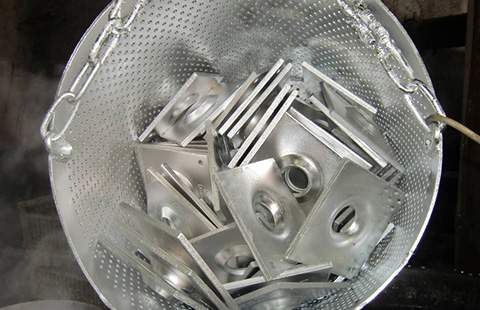
Your advantages at a glance
Optimum protection for small parts
Centrifugal galvanising provides small parts with excellent corrosion protection without sacrificing precision and accuracy of fit. This method is ideal for components where every dimension counts.
Better flow behaviour of the zinc
Compared to conventional hot-dip galvanising, centrifugal galvanising uses a higher zinc bath temperature (approx. 450 °C to 530 °C). This leads to improved run-off behaviour of the zinc from the surface and enables a more even coating.
Mechanically resilient
Our iron-zinc alloy coating surpasses conventional structural steels in terms of hardness, making it more resistant to mechanical influences such as impacts, blows and abrasion. This is particularly valuable during transport, assembly or everyday use.
Edge protection
The zinc coating is particularly thick at the edges, which is favoured by the chemical bond between steel and zinc. This ensures optimum protection even in areas and cavities prone to corrosion.
Atmospheric resistance
Despite the erosion of the zinc coating due to extreme weather conditions, galvanising remains a reliable corrosion protection. The duration of protection can be estimated based on the thickness of the zinc coating and the location of the object.
Cathodic protection
In the event of minor damage to the zinc surface, the surrounding zinc further protects the steel through a chemical reaction. This prevents the zinc layer from rusting underneath
Extremely good adhesion
The alloy layers of zinc and iron created during galvanising are firmly bonded to the steel surface, which ensures excellent adhesion.
Durable, long-lasting protection
Centrifugal galvanizing is maintenance-free and requires no maintenance effort. According to DIN EN ISO 14713, the protection period until the first repair can be more than 100 years, which other corrosion protection systems cannot provide.
Economical corrosion protection
The lifetime costs of centrifugal galvanizing are significantly lower than with conventional corrosion protection systems.
Sustainable, resource-efficient, environmentally friendly
The process of centrifugal galvanizing is resource-efficient and environmentally friendly in all areas.
References
Our references speak for themselves: you will find projects all over Germany, the Netherlands and other neighboring countries in which our galvanized components are used. From the north to the south, from major projects to smaller construction projects – surfaces need corrosion protection. Discover the diversity and durability of our services and see our high quality standards for yourself.
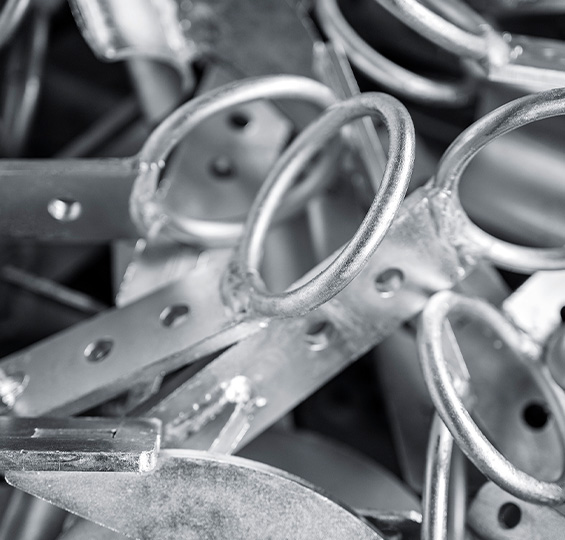
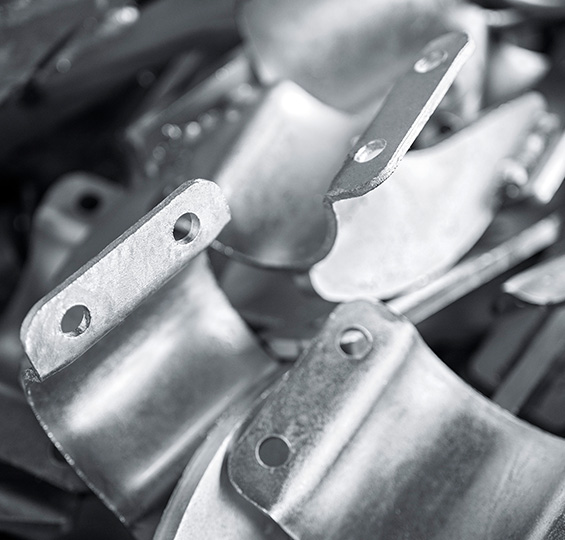
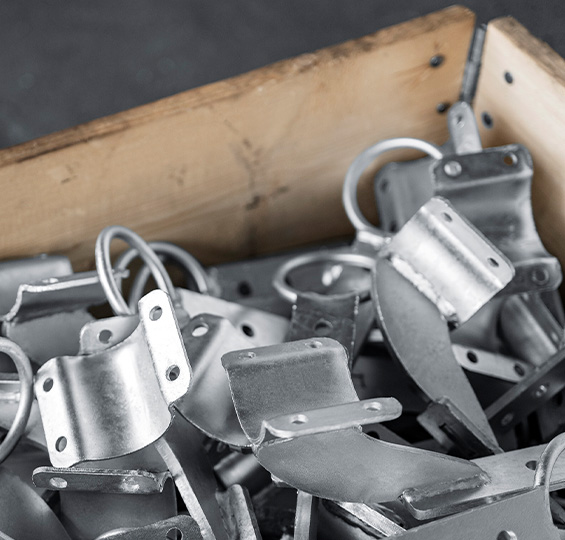
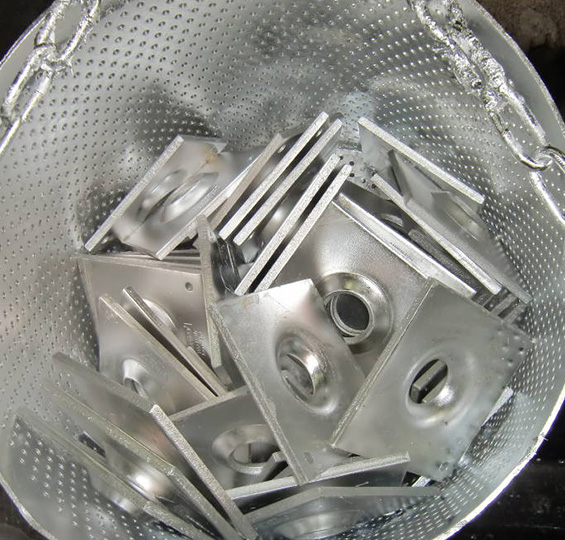
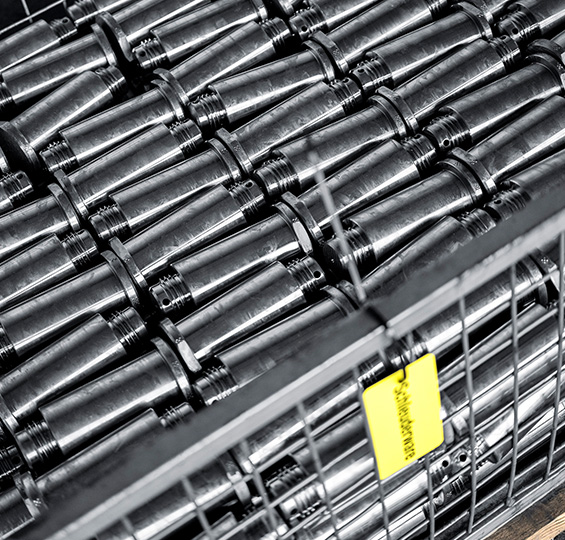
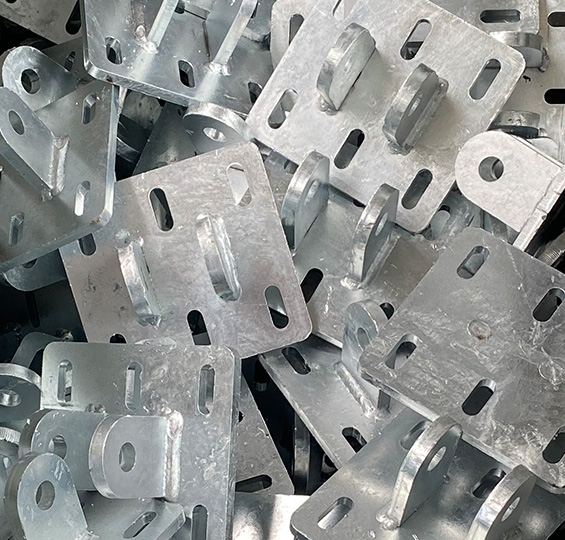
Your questions – Our answers
Which products is centrifugal galvanizing particularly suitable for?
Centrifugal galvanizing is ideal for small parts such as screws, nuts, bulk goods and for products with special surface finish requirements. This method is particularly useful for parts where high precision and accuracy of fit are essential, as it provides comprehensive corrosion protection without compromising the functionality or dimensions of the parts.
How does centrifugal galvanizing differ from standard hot-dip galvanizing?
The main difference between centrifugal galvanizing and standard hot-dip galvanizing lies in the temperature of the zinc bath and in the processing of the parts. With centrifugal galvanizing, we use a higher zinc bath temperature, which allows the zinc to run off better. In addition, excess zinc is removed by the centrifugal process, which ensures a more precise and cleaner zinc coating and is particularly advantageous for small parts.
What are the advantages of centrifugal galvanizing in terms of environmental friendliness?
Centrifugal galvanizing is an environmentally friendly process as it is efficient in its use of zinc and produces little waste. By spinning off the excess zinc, it ensures that only the required amount of zinc is used, which conserves resources. In addition, by precisely controlling the zinc bath temperature and using advanced cleaning technology, our process reduces emissions and environmental impact.
What is the production process for centrifugal galvanizing?
1. The small parts are placed in a specially designed, round basket with numerous drainage openings.
2. After immersion in the zinc bath, the basket is rotated quickly to effectively spin off excess zinc.
3. Finally, the workpieces are quenched in a water bath to prevent the individual components from sticking together.

How can we help?
We have numerous techniques and processes at our disposal that we can use to support you with your project. We would be happy to discuss your requirements in a joint meeting to evaluate how we can best meet your individual requirements.