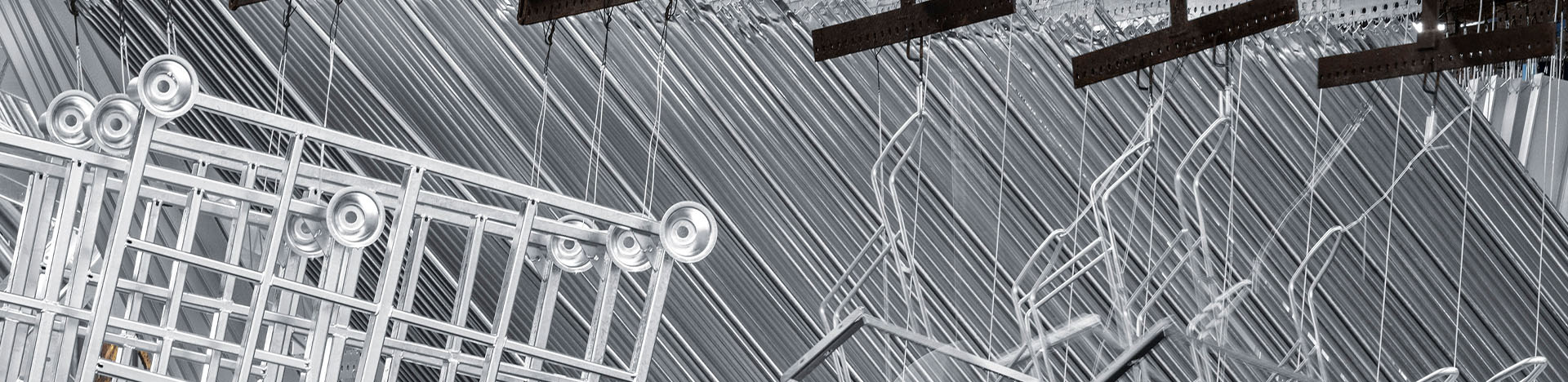
Hot-dip galvanising: The perfect corrosion protection
Due to its exceptional durability, hot-dip galvanising is the optimal method for protecting steel against corrosion. The process is also characterised by being maintenance-free and environmentally friendly, making it an unrivalled solution for corrosion protection.
In hot-dip galvanising, we immerse steel parts in molten zinc, which forms a robust zinc coating on the steel surface. This method offers your products outstanding protection against corrosion, which can last longer than a century in accordance with DIN EN ISO 14713-1. The duration of this protection varies depending on atmospheric, mechanical, chemical and thermal conditions.
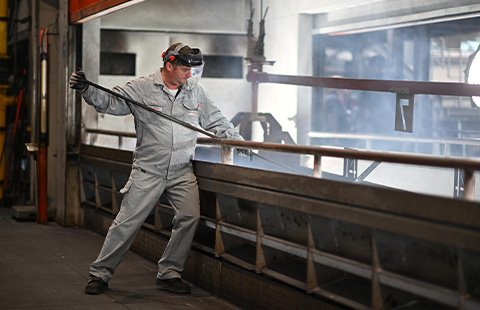
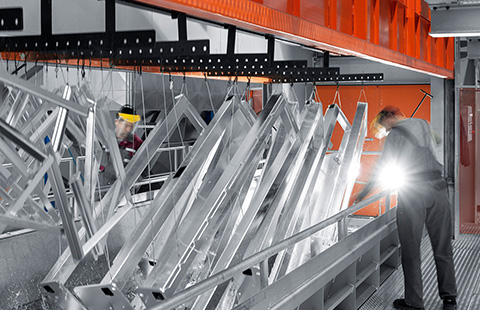
Your advantages at a glance
Mechanically resilient
Our iron-zinc alloy coating surpasses conventional structural steels in terms of hardness, making it more resistant to mechanical influences such as impacts, blows and abrasion. This is particularly valuable during transport, assembly or everyday use.
Edge protection
The zinc coating is particularly thick at the edges, which is favoured by the chemical bond between steel and zinc. This ensures optimum protection even in areas and cavities prone to corrosion.
Atmospheric resistance
Despite the erosion of the zinc coating due to extreme weather conditions, galvanising remains a reliable corrosion protection. The duration of protection can be estimated based on the thickness of the zinc coating and the location of the object.
Cathodic protection
In the event of minor damage to the zinc surface, the surrounding zinc further protects the steel through a chemical reaction. This prevents the zinc layer from rusting underneath
Extremely good adhesion
The alloy layers of zinc and iron created during galvanising are firmly bonded to the steel surface, which ensures excellent adhesion.
Durable, long-lasting protection
Hot-dip galvanising is maintenance-free and requires no servicing. According to DIN EN ISO 14713, the protection period until the first repair can be more than 100 years, which other corrosion protection systems cannot achieve.
Economical corrosion protection
The lifetime costs of hot-dip galvanising are significantly lower than with conventional corrosion protection systems.
Sustainable, resource-efficient, environmentally friendly
The hot-dip galvanising process is resource-efficient and environmentally friendly in all areas.
References
Our references speak for themselves: you will find projects all over Germany, the Netherlands and other neighboring countries in which our galvanized components are used. From the north to the south, from major projects to smaller construction projects – surfaces need corrosion protection. Discover the diversity and durability of our services and see our high quality standards for yourself.
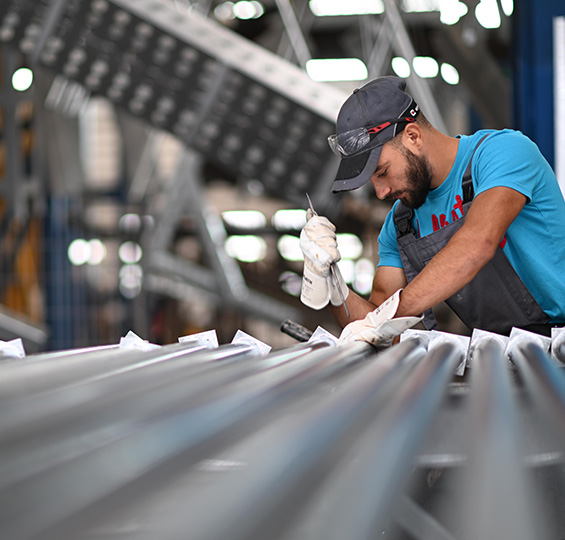
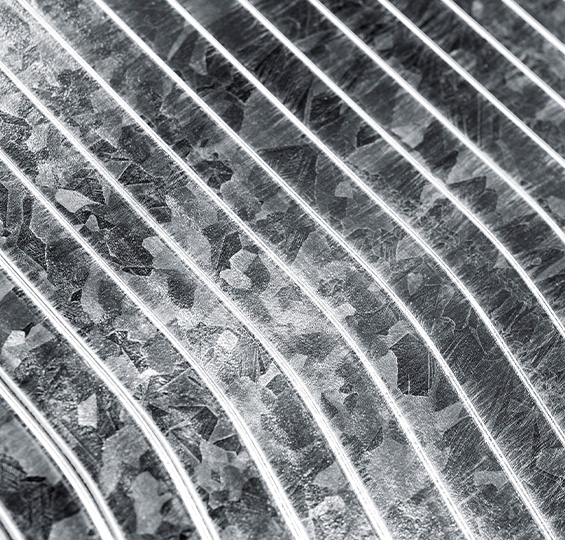
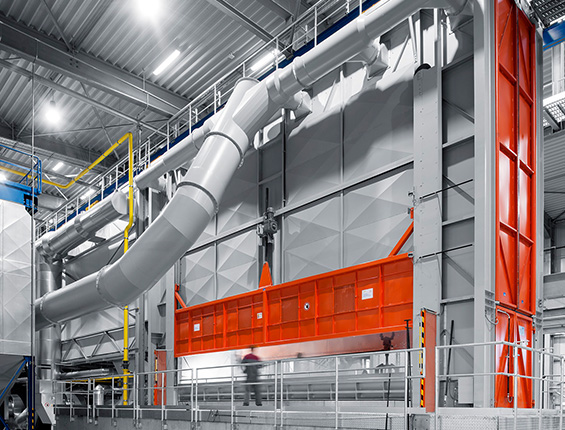
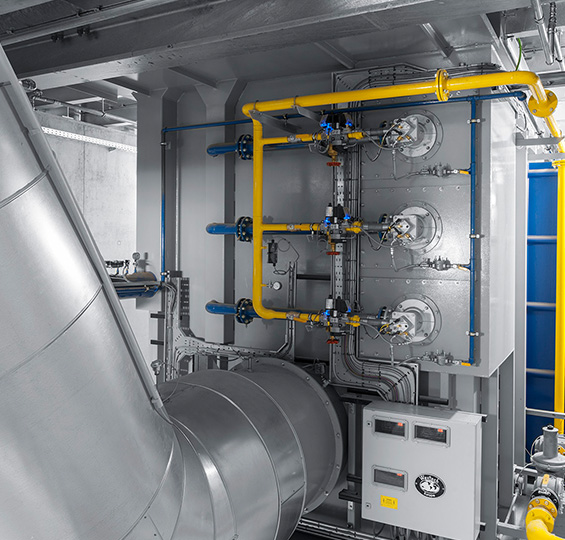
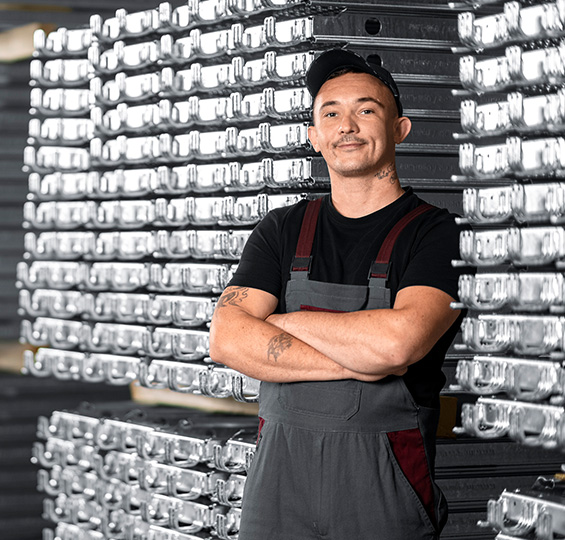
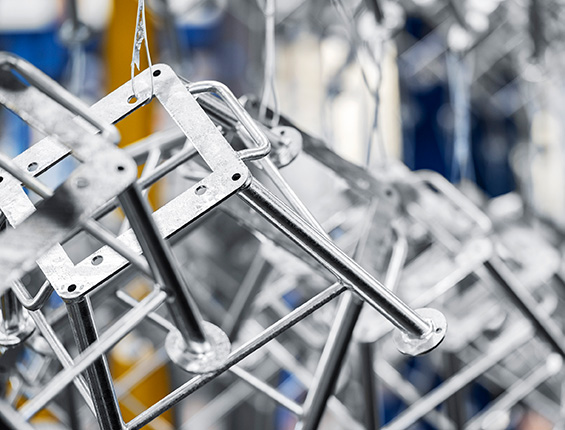
Your questions – Our answers
How long does hot-dip galvanising provide protection?
Hot-dip galvanising is an extremely durable form of corrosion protection. According to the DIN EN ISO 14713-1, Table 2, a protection duration of more than 100 years can be achieved.
Is hot-dip galvanising a reliable procedure?
The zinc covering offers a reliable corrosion protection which is executed industrially and under defined conditions acc. DIN EN ISO 1461. Therefore, the requirements on the properties and reliability of hot-dip galvanising are clearly defined.
Does hot-dip galvanising have to be serviced?
Hot-dip galvanising is maintenance free. Therefore, they are one of the least expensive long-term protection systems (because they protect longer and do not generate subsequent costs). It must be remembered that maintenance work in particular generates additional costs and can also cause problems, in particular in areas which are hard to reach. Maintenance free corrosion protection is therefore worth its weight in gold.
What is the production process for hot-dip galvanizing?
1. Computer-controlled transport technology for precise, consistent and efficient processes.
2. At the control station, all processes within the plant can be tracked at all times and are permanently recorded.
3. A completely enclosed preliminary treatment and cleaning of the exhaust air per scrubber helps to achieve exceptionally low emission values which underrun the limit values multiple times over.
4. Reduced volumes of waste through permanent fluxing agent treatment and separated acid management.
5. Lead-free molten zinc acc. DIN EN ISO 1461 and the DASt directive 022 (zinc bath class 1) for galvanisation in line with the standards and a high-quality appearance of the components.
6. Ultra-modern torch technology for even heat distribution in the molten zinc.
7. Generously-sized hall areas permit efficient processes as well as customer-friendly and variable materials planning.”
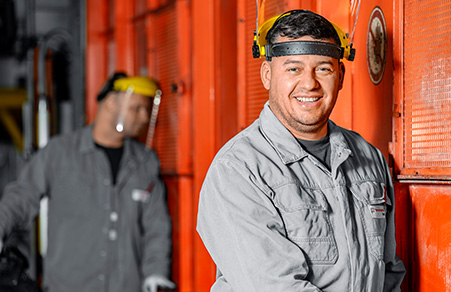
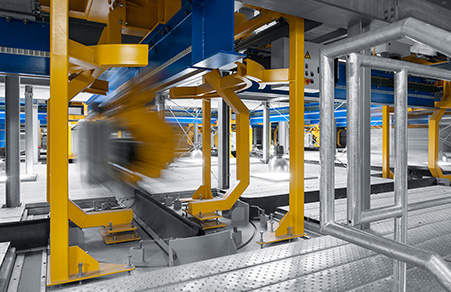
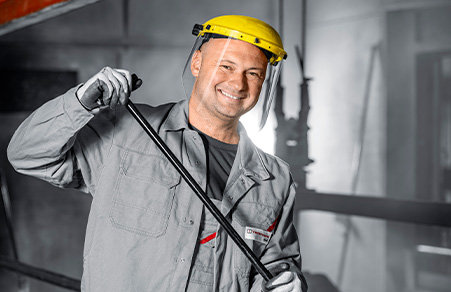

How can we help?
We have numerous techniques and processes at our disposal that we can use to support you with your project. We would be happy to discuss your requirements in a joint meeting to evaluate how we can best meet your individual requirements.