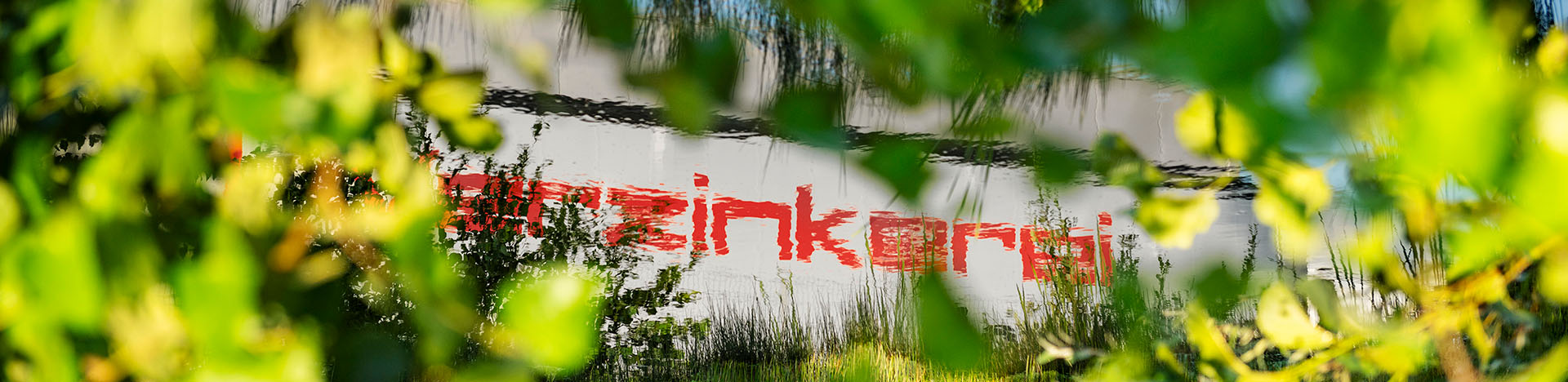
Sustainability is part of our DNA
Part galvanisation is verifiably the most sustainable and environmentally-friendly corrosion protection system with protection durations of up to 100 years (DIN EN ISO 14713). In comparison to conventional coating systems or paint coatings, hot-dip galvanising saves up to 3 times more energy and resources. The ultra-modern systems at the Heek, Stadtlohn and Sulz plants minimise the energy consumption and therefore also the environmental pollution.
Treatment plants, closed materials cycles and ultra-modern filter technology
are the guarantee for optimum and efficient energy utilisation and resource economisation. The Lichtgitter galvanising plants are justifiably proud of the positive environmental balance which is verified through regular emission measurements and environmental inspections through the approval authorities.
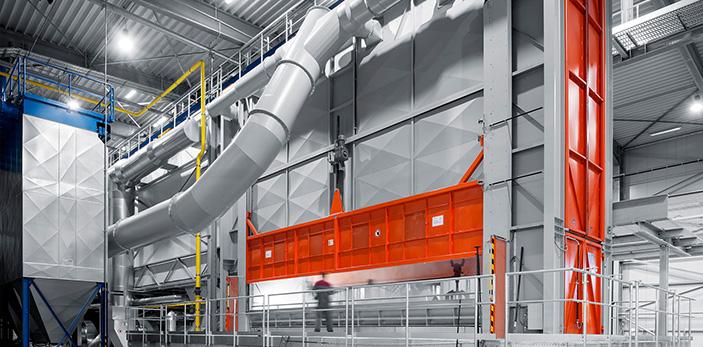

A research project on the “Reduction of the use of zinc during hot-dip galvanisations through the combination of a new fluxing agents with an innovative fluxing agent treatment plant”
was supported in the year 2010 through the Federal Ministry for the Environmental, Nature Conservation and Nuclear Safety. The knowledge gained was consistently implemented in the other galvanising plants within the Group. In this way, a substantial proportion of CO2 emissions are saved at the Heek, Stadtlohn and Sulz galvanising plants.
Use of highly efficient charging management in forklift logistics
This allows us to save energy costs and conserve resources by extending the service life of the batteries.
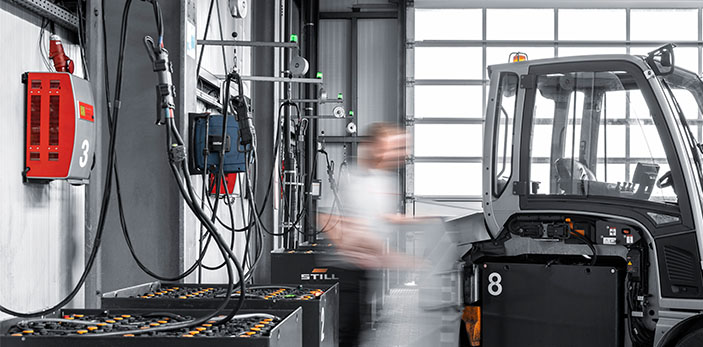
Openness regarding environmental data
Openness regarding environmental data has always been the path taken by the Lichtgitter Group galvanising plants. From this, for example, results a Type 3 Declaration acc. ISO 14025 and EN 15804. The environmental product declaration for hot-dip galvanised construction steels accords with the international standards for environmental accounting.
What measures do we use to achieve environmentally friendly production?
We save on natural gas through the consistent use of the hot furnace exhaust gases to heat the preliminary treatment baths. At the same time we save CO2 emissions totalling 1,000 t per year in comparison to conventional galvanising furnaces. The degree of energy utilisation in our galvanising plants lies at up to 96 percent.
The emission-relevant steps in our galvanising plants have been interlinked and enclosed and kept under permanent negative pressure. This is the best possible way to protect the environment against emissions.
We continuously regenerate the fluxing agent used during the preliminary treatment for galvanisation. In this way, we keep the quality of the fluxing agent at a consistently high level and avoid hazardous goods transportation for the treatment of the fluxing agent.
Tested quality
So that you can utilise our hot-dip galvanisation as extremely durable corrosion protection, we place maximum standards on the quality of the zinc and also of every single processing step. For maximum customer satisfaction, you can also profit from consistently upheld standards, verifiable regulations and innovative further developments in our galvanising plants. Through the maintenance of the following norms and standards, we guarantee you market-leading, certified quality:
DIN EN 1461: “Zinc coverings applied through hot-dip galvanising on steel” (part galvanising)
DIN EN ISO 9001 (Quality Management System)
DIN EN ISO 50001 (Energy Management System)
EN 1090: “Monitoring of the plant’s own production inspection of hot-dip galvanising acc. EN 1090”
DASt directive 022: “Hot-dip galvanising of supporting steel constructions”
Member of the Hot-dip Galvanisation Industrial Association
“DIN EN ISO 3834: “Fulfillment of welding requirements”
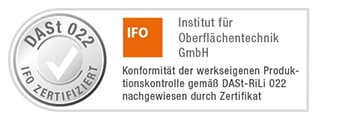
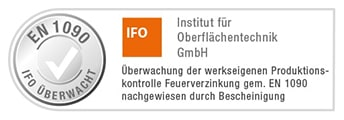
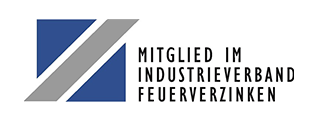
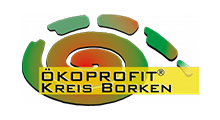
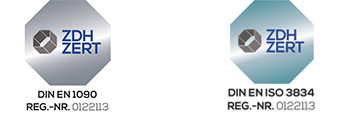
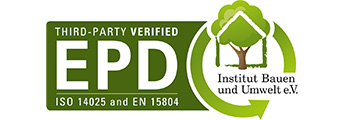
Environmental Product Declaration
An EPD is a documented, transparent and comparable information format that describes the environmental impact of a product over its entire life cycle. It is based on internationally recognized standards and is verified by independent third parties to ensure the accuracy and reliability of the data provided. EPDs serve as an important source of information for architects, engineers and building owners to make sustainable decisions when selecting building materials and to enable building certifications.
To use the EPD effectively, stakeholders should refer to it as a comprehensive source of information on the environmental impact of hot-dip galvanized steel throughout its life cycle. It can be used by architects, engineers and builders to compare materials based on verified environmental data and make decisions that minimize the environmental footprint. However, the EPD should not be used as the sole determinant for material selection without considering specific project requirements, local regulations and other sustainability criteria. It should also be noted that the EPD is not intended for direct comparison with other materials, as such comparisons require consistent and equivalent methodological frameworks.
The EPD covers galvanized steel products of grades S235 to S500 intended for bolted, welded or otherwise connected constructions of buildings, bridges and other structures or in composite structures made of steel and concrete. It is valid for profiles and commercial bars of various grades and delivery forms that have been hot-dip galvanized in accordance with EN ISO 1461 and DASt Guideline 022. The EPD was prepared in accordance with the product categories for structural steels and the requirements of EN 15804+A2 and covers the period from April 29, 2024 to April 28, 2029. Members and partners of the Industrieverband Feuerverzinken e.V. can use this EPD and download it under the following link: Download EPD
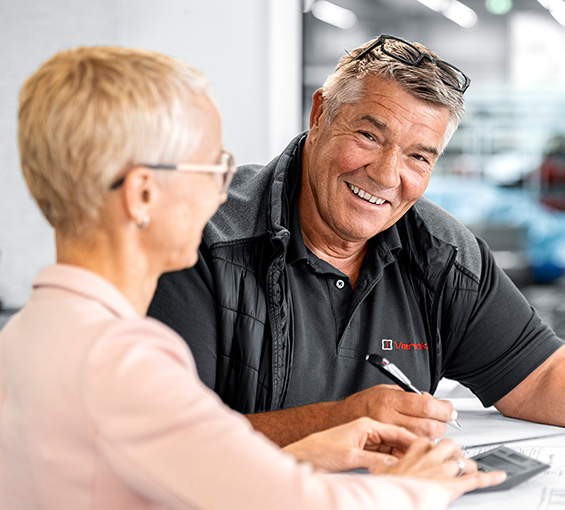
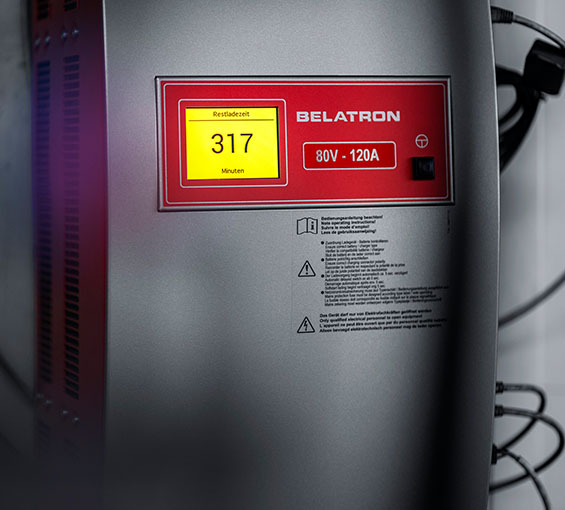
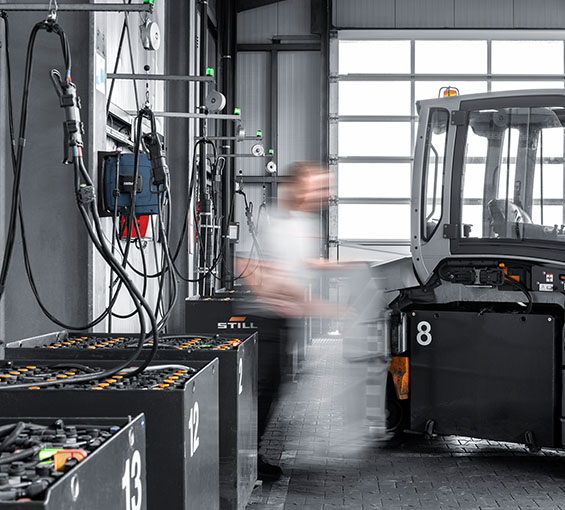
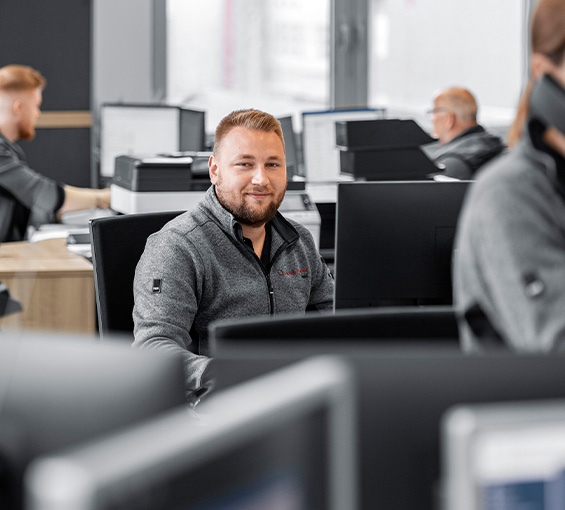
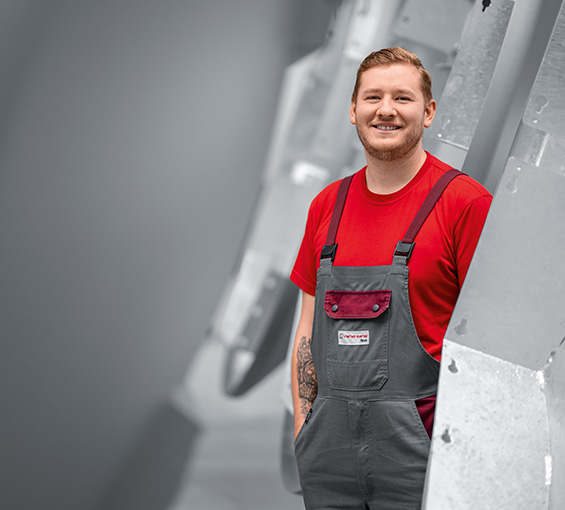
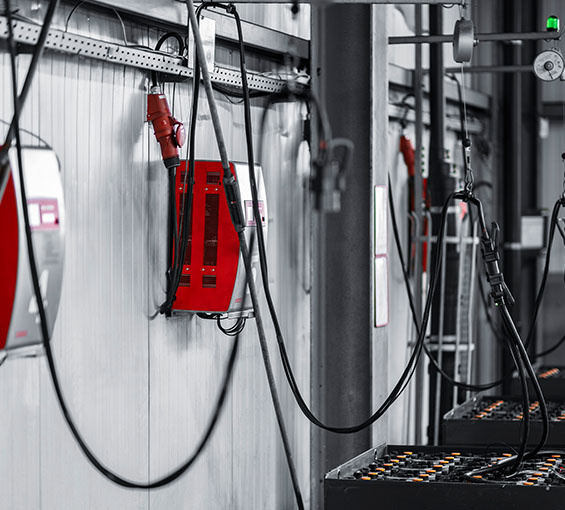

How can we help?
We have numerous techniques and processes at our disposal that we can use to support you with your project. We would be happy to discuss your requirements in a joint meeting to evaluate how we can best meet your individual requirements.